I. Verification
4. Solution of numerical benchmark for
thermal and viscous flows [7]
- Figure 1 shows the velocity
and temperature fields of obtained solution for defined problem. Two main circulations are clearly
visible: an
upper clockwise circulation transporting hot liquid towards the top
wall and
back along the isotherm of the density extremum, and a lower
counter-clockwise
circulation within the cold wall region. At the cold wall, the
descending hot
liquid interacts with the rising cold liquid. This creates a distinct
saddle
point in vicinity of the wall, approximately at about two-thirds of the
cavity
height. Position of the saddle point, given by the balance of competing
positive and negative buoyancy forces, appears to be very sensitive to
inaccuracies of the numerical solutions.
Figure
1.
Natural convection of water.
Temperature and velocity field for the fine mesh solution of FRECON3V
(run
FRE6)
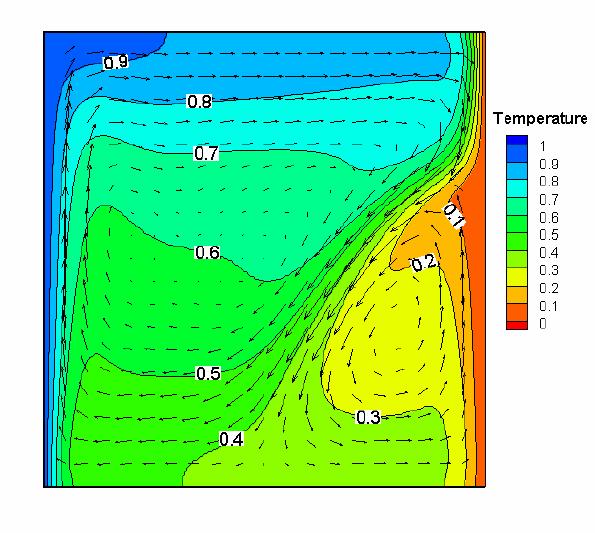
- In order to compare performance of
different codes in terms of their ability to reproduce fine details of
the flow
structure it is not sufficient to verify agreement of global flow field
parameters,
like those given in Tables 2-6. It appears that small deviation in
their value
(2% - 5%) from the reference solution, usually reported as reasonable
or
even excellent agreement, corresponds to distinct changes of
the flow
pattern. Such changes become responsible for differences in the local
mass and
heat transfer in the system. These effects can be perhaps neglected if
only
insulation or heat drainage are of the main interest. But they are not
tolerable when phase change processes are present (e.g. freezing of
water) or
transport of small inclusions is an important issue.
- Hence, to obtain
better insight into differences or similarities of the flow structures
obtained
from the investigated solvers, the second step of the verification
procedure is
proposed. It is based on calculating deviation of the velocity profiles
extracted along three selected lines: horizontal centreline y=0.5,
vertical
centreline x=0.5 and vertical line passing through the mixing zone and
the
stagnation point at the cold wall (x=0.9). Locations of the lines are
selected
in such way that for any investigated mesh resolution they still match
the
nodes location, and additional interpolation errors are avoided. Figure
3 shows
example of the velocity profiles along the horizontal and vertical
symmetry
lines of the cavity for meshes from Table 2. It is worth noting that
the errors
of the simulation performed for the quite fine mesh (FRE2) may reach
almost 50%
for the vertical velocity (Fig. 3a). Also large errors are present for
the
horizontal velocity component obtained for the coarse mesh (Fig. 3b).
This test
indicates that modelling of a simple natural convection in the presence
of the
strongly non-linear variation of water density requires careful
analysis of
results and very fine meshes.
-
Figure3. Velocity profiles extracted
for
the horizontal centre-line Y=0.5
(a)
– vertical velocity
component
(b)
- horizontal velocity component
- The mesh sensitivity analysis
performed for five investigated codes gives us some reference about
convergence
rate and allows to estimate their asymptotic behaviour. For more
detailed
comparison the flow field obtained using FRECON3V for
the fine mesh (201x201) was selected. The
velocity and temperature profiles extracted along above mentioned lines
are
approximated with the high order polynomial and treated as a reference
(benchmark) solution. The numerical values of the polynomials
coefficients are
given in Appendix. The fifteen digit accurate values of the
coefficients are
given to ease comparisons in the future. Obviously, it will be easier
to quantify
accuracy using well defined analytical functions than by overlapping
reproduced
figures.
- An assessment on the accuracy of the
solution
is obtained calculating relative differences in terms of defined below
standard
deviations s, evaluated for
the polynomials
describing benchmark profiles and corresponding values extracted from
the
interrogated solution:
(4.1)
- Here, N gives number of discrete
points (corresponding to the discretization nodes) of the interrogates
solution, w(xi) polynomial value of the benchmark solution
for the
point xi , and f(xi) value of the analyzed
discrete
solution for the point xi.
- Nine indicators are defined according
to the
above definition and used to evaluate accuracy of the solutions: σu1,
σw1, σt1, σu2,
σw2, σt2, σu3,
σw3 and σt3. They describe standard deviations calculated
for two velocity components U ,W and temperature T for
profiles
extracted at centrelines Y=0.5, X=0.5,
and vertical line X=0.9.
- The proposed accuracy indicators can
be easily used to assess performance of any numerical solutions,
regardless of
dimension of the mesh size, as well as to estimate the rate of
convergence of
successive solutions. Data collected in Table 7 are presented in Figure 4. The figures show, respectively,
mesh dependence of σ u1 , σ w1 for
velocity profiles at
Y=0.5, σ u2 , σ w2 for
velocity profiles at X=0.5, σ u3, σ w3 for
velocity
profiles at X=0.9, and σt1 , σt2, σ t3 for
three temperature profiles at Y=0.5, X=05
and X=0.9.
- The
value of σ u1 , σ
w1 , σ u2
σ w2 ,
σ u3, σ w3 , σ
t1 ,σ t2 ,σ t3 for the fine
mesh FRECON solution
(FRE6) was taken as a reference error indicator. Generously setting
cut-off
value for standard deviation equal 3 we come to conclusion that only
solutions
FRE4-7 and FLU3 are close enough to the reference solution to be
assumed as the
correct ones.
- From Figure 4 it is easily visible
that the
rate of convergence of SOLVSTR is much slower in comparison with
FRECON. From
the other hand, analysing the values of the
indicators on successive meshes we may find that the rate of
convergence for FLUENT, FIDAP is almost linear in contrast to the much
faster
convergence of FRECON or even SOLVSTR. It is rather surprising as the
both
commercial codes claim to use second order approximations.
- The stream function - vorticity
solver SOLVSTR
needs almost triple mesh refining (250x250) to reach accuracy
comparable with
that of other “mesh related” codes. One of the possible
explanations of such
behaviour is the lack of “upwind” schemes in SOLVSTR code.
Moreover,
improvement of the ADI algorithm and replacement of Gauss-Seidel
algorithm by
relaxation methods like SOR, CG, GMRES, could lead to better
performance of the
code.
- It is
worth noting that convergence of temperature is relatively easy to
reach, and
even for the most coarse meshes temperature profiles are practically
“exact”.
It indicates robustness of the energy equations and relatively small
effect of
the convective term on the resulting temperature distribution. It is
rather
surprising result, and it suggest that use of temperature as a
convergence
indicator can be dangerously misleading. At least for the analysed flow
configuration.
- A mesh-free code SOLVMEF using diffuse approximation
fails this very
sensitive test of accuracy. On the other hand the extremely long time
of
calculation does not allow for mesh refinement to increase the
accuracy. Global
and average indicators show proper trend of convergence. However, the
main
disadvantage of this method, its slow rate of convergence, is still
challenging
for future research.
Figure 4. Mesh dependence:
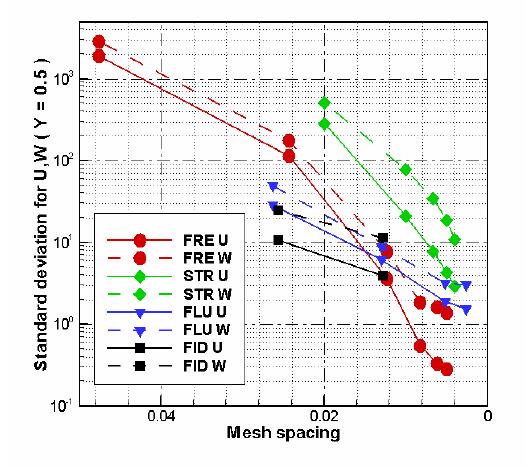
(a)
– standard deviations σ u1 , σ w1 for
velocity profiles
at Y=0.5;
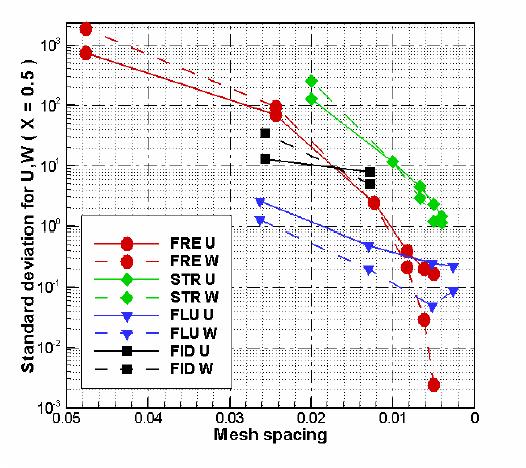
(b)
- standard deviations σ u2 , σ w2 for velocity profiles at X=0.5,
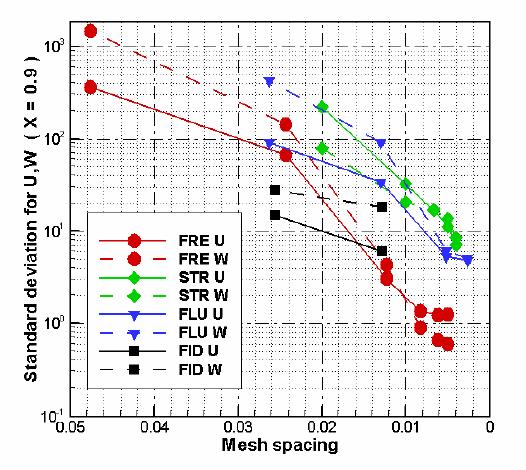
(c)
-
standard deviations σ u3, σ w3 for
velocity profiles at
X=0.9;

(d)
- standard deviations σt1 , σt2, σ t3 for
three temperature profiles at Y=0.5, X=0.5
and X=0.9.